Horizontal Directional Drilling Explained: A Complete Guide for Efficient Trench less Solutions
- Grid Tech
- Sep 26, 2024
- 5 min read
Horizontal Directional Drilling (HDD) has revolutionized the construction and utilities industries, providing an efficient, cost-effective, and environmentally conscious solution for installing underground pipelines and cables. This trench less technology allows for the installation of utilities under obstacles such as rivers, roads, and urban infrastructure without the need for disruptive open-cut excavation. In this article, we delve deep into the process of HDD, its applications, benefits, and technical considerations.

What is Horizontal Directional Drilling?
Horizontal Directional Drilling is a trench less drilling technique used to install pipelines, conduits, or cables underground. The process involves a drilling rig that bores a horizontal path beneath the surface, avoiding the need for large trenches. HDD is particularly useful for projects that require minimal surface disruption, such as in urban areas or sensitive environmental zones.
The HDD Process: A Step-by-Step Overview
The Horizontal Directional Drilling process is typically broken down into three main phases: pilot hole drilling, reaming, and product installation.
1. Pilot Hole Drilling
The HDD process begins with the drilling of a pilot hole along a predetermined path. Using a directional drilling rig, operators guide the drill head under the ground, steering it with precision to follow the planned trajectory. The drill head is equipped with sensors that provide real-time data on its position, angle, and depth. This allows the operators to make constant adjustments, ensuring that the drill remains on course.
2. Reaming
Once the pilot hole is completed, the next step is reaming. This process involves enlarging the pilot hole to accommodate the pipe or conduit. A reamer is attached to the drill string, which rotates and grinds away soil and rock, widening the hole. The size of the reamed hole is carefully calculated based on the diameter of the pipe that will be installed. Multiple passes may be required to achieve the desired hole diameter.
3. Product Installation
The final stage of HDD is the pullback phase, where the product (pipeline or conduit) is installed. The pipe is attached to the reamer, and as the reamer is pulled back through the hole, it drags the pipe into place. The pipeline is typically pre-welded and laid out on the surface prior to this step, ensuring a smooth installation.

Applications of Horizontal Directional Drilling
Horizontal Directional Drilling is widely used in various sectors, including oil and gas, telecommunications, water and sewage, and electrical transmission. Its versatility allows it to be employed in a range of environments and for different types of infrastructure projects. Some common applications include:
Oil and Gas Pipelines: HDD is frequently used to install oil and natural gas pipelines beneath rivers, highways, or densely populated areas, where open-cut trenching would be impractical.
Telecommunications: HDD enables the installation of fiber optic cables and other communication networks with minimal surface disruption, making it ideal for urban installations.
Water and Sewer Lines: Municipalities rely on HDD for the installation of water and sewer lines, particularly in areas with pre-existing infrastructure or sensitive environmental conditions.
Electrical Conduits: Horizontal Directional Drilling provides a seamless solution for installing high-voltage electrical cables underground, reducing the visual impact of overhead lines.

Benefits of Horizontal Directional Drilling
Horizontal Directional Drilling offers a variety of advantages over traditional open-cut excavation methods. These benefits make HDD an increasingly popular choice for infrastructure projects, especially in challenging environments.
1. Minimal Surface Disruption
One of the most significant benefits of HDD is its ability to minimize surface disruption. By boring beneath the surface, HDD avoids the need to excavate large trenches, preserving existing infrastructure and reducing the impact on traffic, landscapes, and local communities.
2. Cost-Effective
While the initial setup for HDD may be higher than traditional methods, the overall cost savings are substantial. HDD reduces the need for surface restoration, traffic management, and environmental remediation, all of which contribute to lower project costs in the long run.
3. Environmentally Friendly
Horizontal Directional Drilling is considered an eco-friendly technology due to its reduced environmental footprint. By drilling beneath the surface, HDD minimizes the amount of soil displacement and vegetation removal, preserving natural habitats and ecosystems. Additionally, the reduced need for excavation helps limit the release of greenhouse gases.
4. Safe and Efficient
HDD is a safe and efficient method for installing underground utilities. With advanced guidance systems, operators can accurately control the drill's path, reducing the risk of accidents and damage to nearby infrastructure. The entire process is also quicker than traditional excavation methods, enabling projects to be completed in a shorter timeframe.
5. Versatility
Horizontal Directional Drilling is highly versatile and can be adapted to a wide range of soil conditions, including rocky terrain, clay, and sand. This adaptability allows HDD to be used in various locations, from urban environments to rural areas with minimal limitations.
Technical Considerations in Horizontal Directional Drilling
Successful Horizontal Directional Drilling projects depend on several key technical factors. Proper planning and execution are crucial to ensure the project is completed safely, efficiently, and within budget. Below are some of the main technical considerations that should be taken into account when undertaking an HDD project.
1. Soil Conditions
Understanding the geological conditions of the site is critical for the success of any HDD project. Different soil types present unique challenges, and the drilling equipment and techniques must be selected accordingly. For example, rocky terrain requires more powerful reaming tools, while soft soils may necessitate the use of drilling fluids to maintain hole stability.
2. Bore Path Design
The design of the bore path is essential for ensuring a smooth drilling process. The path must be carefully planned to avoid underground obstacles, maintain a consistent depth, and minimize bends and curves. A well-designed bore path reduces the risk of equipment failure and ensures the safe installation of the product.
3. Drilling Fluids
Drilling fluids, commonly referred to as drilling mud, play a vital role in the HDD process. These fluids help to stabilize the borehole, lubricate the drill head, and remove cuttings from the hole. The type and composition of drilling fluids used will depend on the soil conditions and the size of the borehole.
4. Equipment Selection
Choosing the right equipment for an HDD project is another key factor in its success. The drilling rig, drill pipes, reamers, and drill heads must be selected based on the size of the project and the specific conditions of the site. Using the right equipment not only ensures efficiency but also reduces the risk of breakdowns and delays.
5. Safety Measures
Safety is always a top priority in any drilling project. HDD crews must follow strict safety protocols to protect both workers and the surrounding environment. This includes monitoring the drill path to avoid hitting underground utilities, using protective equipment, and ensuring that the drilling fluids are properly managed to prevent environmental contamination.
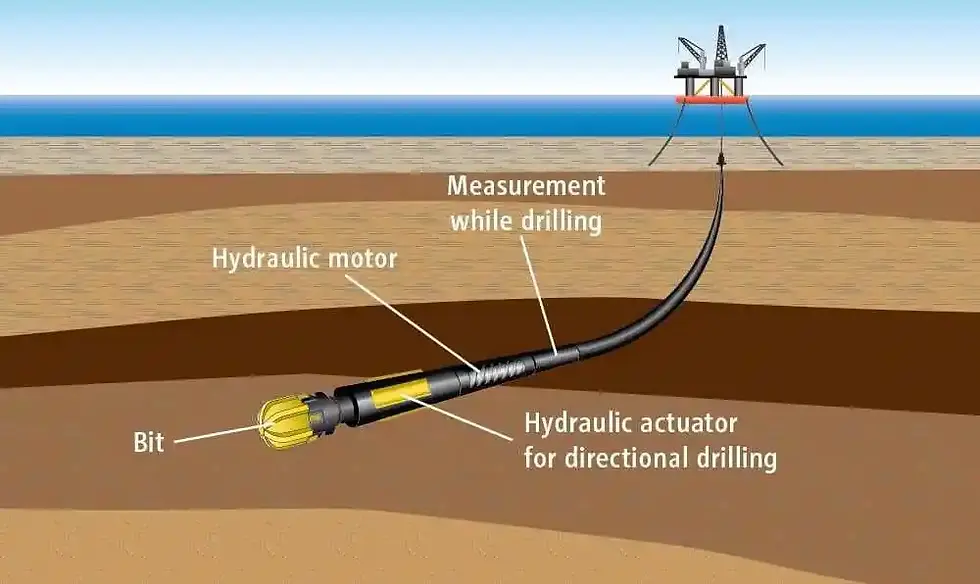
Conclusion
Horizontal Directional Drilling is a cutting-edge technique that has transformed the way we install underground utilities. Its numerous benefits, including minimal surface disruption, cost-effectiveness, and environmental advantages, make it an invaluable tool for a wide range of industries. By understanding the HDD process, its applications, and the technical considerations involved, we can ensure that our projects are completed successfully and with minimal impact on the environment.
Comments