7 Benefits of Directional Boring as a Digging Technique
- Grid Tech
- Oct 19, 2022
- 3 min read
Other names for directional boring include horizontal drilling, deviated drilling, and horizontal directional drilling (HDD). The phrase "horizontal directional drilling" is frequently used to refer to large-scale projects that call for more powerful equipment. In general, directional boring entails the employment of underground boring equipment that is launched from the surface to excavate precise, predetermined subsurface pathways. Because of its efficiency and other advantages, directional boring is becoming a more popular choice among energy businesses and oil and gas corporations than conventional trenching.
Particularly in the oil and gas industry, underground boring is frequently employed to drill wells through rock.
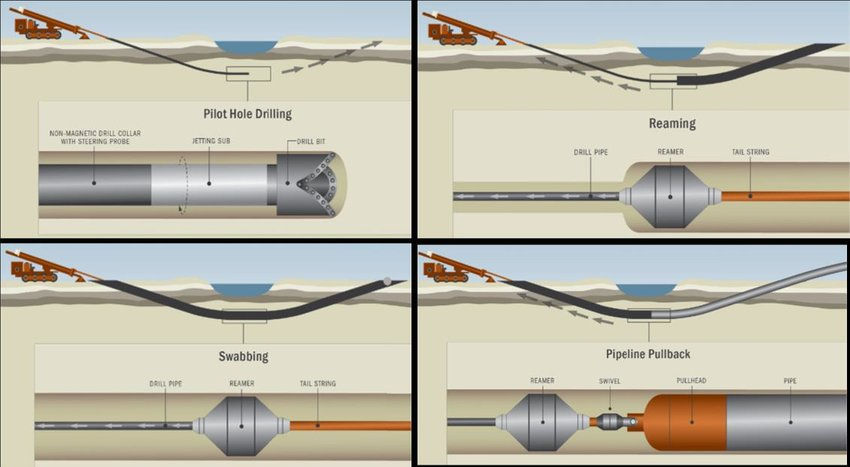
Another excellent technique for drilling into the ground to install pipes and utilities is underground boring. This is because it causes the least amount of surface disturbance while excavating precisely along the required line. To create crossings beneath roadways and waterways where pipes can be put, directional boring is frequently used. Here are seven factors to think about if you're curious about some of the unique benefits that directional boring provides:
It doesn't disturb the surrounding area or the land: The biggest benefit it provides over conventional trenching is this. Trenching is not recommended for digging close to houses and other structures or in areas where the earth cannot be disturbed (such as busy roads). By adopting directional drilling, it is possible to excavate beneath roads, buildings, and other infrastructure without harming anything above ground. Additionally, it enables the laying of pipes below rivers and other large bodies of water. Traditional trenching is unable to accomplish this.
2. It's more environmentally friendly.
Compared to trenching, it reduces groundwater pollution. Additionally, it doesn't harm the local ecosystem at the digging site. Additionally, compared to trenching, it causes fewer cracks in rocky locations, protecting and conserving rock formations.
3. Combining it with conventional trenching is useful.
Because of its greater operational costs, directional boring hasn't completely supplanted conventional trenching in terms of popularity. However, directional boring is frequently used in conjunction with trenching in construction projects. The majority of the work may be completed with conventional trenching, and then underground boring may be employed for precise digging beneath or around obstructions.

4. It's a more secure option.
Trenching presents dangers to site safety and necessitates the adoption of protective equipment to avoid catastrophic mishaps. Please read our earlier article on the topic for some trenching safety advice. Making sure workers are safe in the trenches requires a lot of work. Workers are significantly less likely to fall or have to cope with boulders and debris falling around them because directional boring creates a precise path that causes the least amount of ground disturbance. Additionally, directional boring is secure in any weather. When it is raining, snowing, or has recently rained, trenching is dangerous. Naturally, this also means fewer weather-related interruptions to dig projects and project completion without unforeseen delays.
5. It is quicker.
As previously indicated, trenching is much slower and less effective than directed boring, which is theoretically more expensive. When using directed boring, less soil is moved, less soil needs to be replaced, and less soil needs to be disposed of and dealt with after digging is finished. Cleaning up after underground boring is simple. Because time is money, this expedites the process, and directional boring's efficiency may in certain cases offset its higher initial costs. In connection with that, underground boring also needs fewer operators and employees. This allows workers who would have been trenching to work on other parts of the project, speeding up the process even more.

6. Reduced Risk Of Disruption
The two main issues that disrupt the majority of drilling projects—duration and landscaping—are fully eliminated with HDD tooling. Since a horizontal directional drill rod is intended to be more precise, it moves very little soil and doesn't necessitate digging into the ground, keeping any landscaping largely intact. Most people can now complete their drilling tasks and resume their normal operations without too many interruptions thanks to this.
7. Lower Probability Of Soil Contamination
Horizontal underground boring, in contrast to typical drilling, aims to shift soil to its side rather than raise it to the surface. This practically means that there is a far lesser possibility of any soil contamination during drilling spreading above ground. Additionally, this stops contaminated dirt from penetrating the pipes and endangering their structural integrity.
Used heavy machinery such as vibratory hammers, dozers, and other items are all available for purchase and sale from Gridtech. We also assist clients in the purchase and sale of pre-owned goods including steel pipe and broad flange beams.
Although we continually update all of our listings, if you still can't find what you're searching for, you may make a free wanted listing.
Please contact us on call if you have any questions regarding underground boring or would like more information, or send an email.
Comentarios