A step guide to directional drilling
- Grid Tech
- Mar 29, 2023
- 4 min read
Directional drilling is a process in which a well is drilled at an angle, rather than directly down into the ground. It involves drilling a vertical wellbore, and then gradually bending the drill bit to drill horizontally. This process is used in many industries, including oil and gas, mining, and construction. In this blog, we will explore the directional drilling process and its benefits.
The directional drilling process begins with the drilling of a vertical wellbore. This is done using a drilling rig, which is a large machine that is designed to drill into the ground. Once the vertical wellbore has been drilled, the drill bit is then gradually turned to drill at an angle. This is done using a series of special tools and techniques that allow the drill bit to be guided in the desired direction.
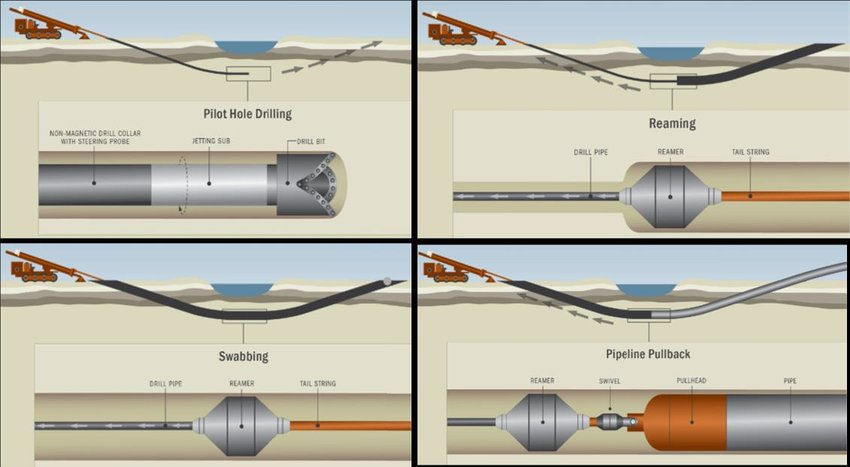
One of the most important tools used in directional drilling is the rotary steerable system (RSS). This system allows the drill bit to be guided in the desired direction using a combination of sensors, computers, and hydraulic systems. The RSS is capable of making small adjustments to the drill bit's direction in real-time, ensuring that it remains on the desired course.
Another important tool used in directional drilling is the measurement-while-drilling (MWD) system. This system is used to measure various parameters while the well is being drilled, such as the direction of the wellbore, the temperature and pressure of the drilling fluid, and the presence of any underground obstructions. This information is then used to make adjustments to the drilling process, ensuring that the well is being drilled in the most efficient and effective way possible.
There are several benefits to using directional drilling. One of the primary benefits is that it allows for the drilling of wells in areas that would otherwise be difficult or impossible to access. For example, directional drilling can be used to drill wells under bodies of water, through mountain ranges, or in areas with limited surface access. This makes it possible to extract resources from areas that would have otherwise been off-limits.
Another benefit of directional drilling is that it can increase the productivity of a well. By drilling horizontally, it is possible to access more of the reservoir, allowing for a greater volume of resources to be extracted. This can lead to increased profits for companies that are involved in the extraction of natural resources.

Horizontal Drilling Rig Components
With respect to the actual apparatus, there are two or three parts that are exclusively subject to the general exhausting arrangement. These are the drill pole and bores. Boring bars, otherwise called drill stems, arrive in different lengths generally regularly 3.0, 4.6, and 9.1 meters. The fragments have female and male stringing on furthest edges to take into account the connection to each other.
In general pole length is determined in light of the section and leaves points in degrees, profundity in meters, length of an obstruction to be avoided, and bend span in meters for both the passage and leave point. Estimations should be viewed as cautiously as surpassing the twist range can make harm the pole and inevitable disappointment. Disappointment brings about extra expenses for substitution and free time of the machine.
The sort of rock laborers are boring decides the decision of the drill head. For delicate ground, like mud, delicate limestone, shale, unconsolidated sand, and red bed, a drag or fixed shaper bit is ideal. These pieces are a solitary strong piece that pivots with the drill string. There are no course and laborers can utilize either slicing liquid or air to eliminate gotten things started.
For medium or hard ground, like limestone, calcites, cherty limestone, hard shale, mudstone, or dolomites, a three-cone moving shaper is ideal. The shape, point and material decide their utilization. Bits with long generally separated teeth are for the medium ground while more limited, firmly dispersed teeth are made to separate hard soil.
Directional drilling can also be used to reduce the environmental impact of drilling operations. By drilling horizontally, it is possible to access resources from a single wellbore, rather than having to drill multiple vertical wells. This reduces the amount of land that needs to be cleared and reduces the overall impact on the environment.

In addition, directional drilling can be used to reduce the cost of drilling operations. By drilling horizontally, it is possible to access resources from a single wellbore, which can significantly reduce the cost of drilling and completing the well. This can lead to increased profits for companies and can make it possible to access resources that would have otherwise been too expensive to extract.
In conclusion, directional drilling is an important process that has many benefits. It allows for the drilling of wells in areas that would otherwise be difficult or impossible to access, increases the productivity of a well, reduces the environmental impact of drilling operations, and can reduce the cost of drilling operations. As technology continues to improve, it is likely that directional drilling will become even more important in the extraction of natural resources.
Comments