Why Horizontal directional boring is valuable?
- Grid Tech
- Jan 29, 2023
- 4 min read
Horizontal directional boring (HDB) is a trenchless construction method used to install underground
pipes, conduits, and cables. It is also known as directional drilling, utility tunneling, and horizontal
directional drilling (HDD). HDB is a versatile and cost-effective method for installing underground
infrastructure.
HDB is used to install pipes and cables in difficult to access areas and under roads, rivers, and other
obstacles without having to dig trenches. The method works by drilling a pilot hole in the ground and
then using a reamer to enlarge the hole. This allows a pipe or cable to be inserted into the hole and
pulled back to its desired location.

What is Horizontal directional boring
Techniques for directional drilling have been used for about a century already. Angles, turns, and
subsurface distances reached in recent years have required extraordinary engineering marvels due to
advancements in technology.
Multilateral, horizontal, and extended reach drilling (ERD) are examples of enhanced oil recovery (EOR)
methods that can significantly boost a downhole's yield. ERD experts have the ability to drill for more
than 10 kilometres (6.2 miles). Petroleum engineering students frequently see images and schematics
that resemble tree roots. The roots' potential directions are limitless if we consider the rig to be the
tree's trunk. Multilateral drilling is akin to the branches of the roots.
Why is the technique so valuable?
The same rig can drill multiple down holes, minimising surface disruption and environmental effect.
These boreholes can also reach depths of up to a mile and, at shallower angles, more than five miles. An
oilfield with dispersed reserves can have a wide radius tapped, making the most of the rig's pricey asset.
One rig operating up to five or ten square miles is much more cost-effective than having a dozen or
more vertical rigs, which may or may not be tapping into the same accessible reservoir deposits. Rigs
and employees have day rates that go into the hundreds of thousands of dollars.
Underground pockets of resources are referred to by names like "oil reservoir" or "hydrocarbon
reservoir" by geologists and engineers. Scientific terminology provides a label to aid in communication,
but Mother Nature has distinct views about how she arranges things.
Seismic geologists, geoscientists, exploration engineers, and CAD specialists work together to provide
the best estimate of the location of potential oil and gas resources. Their projections are supported by a
variety of surveys and prior knowledge. They are unlikely to identify the precise location where they
could have the most resources available to them.
When we observe water reservoirs, we have the mental image of sticking a huge straw in the centre and
squeezing the whole lake. We might have an incorrect impression of the geography of an underground
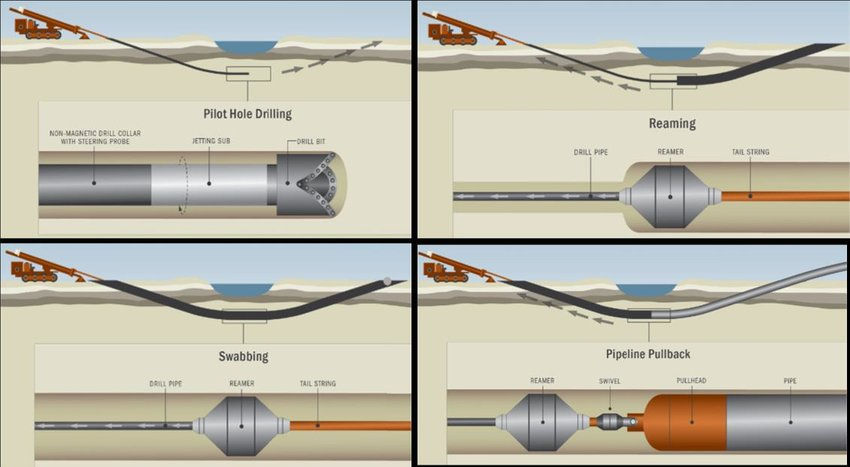
reservoir due to the water's flat surface area and the likelihood of dams and walls that were constructed
by humans. A better view of the resource's random geometry would be possible from the lake's bottom.
You might only be able to extract a small amount of water, for instance, if your fictitious straw occurred
to come into contact with a thin gravel bar in the centre of the lake.
There are other other possibilities in addition to this randomness pertaining to the upper, lower, and
exterior dimensions:
Since reservoirs tend to build horizontally (between formations) rather than vertically, more of the
reservoir can be investigated by drilling at an angle.
The deposit could be oil-saturated sand or shale and not at all resemble a reservoir. Shale is an excellent
material for directional drilling because it allows exploration of the formation to follow richer seams.
The hydrocarbons are separated from the surface by a hard rock, such as granite.
Other factors, such as the surface land being a town, mountain, nature reserve, or area of special
scientific interest, prevent access to the reservoir from above (SSI).
Instead of accumulating in a single deposit, the oil and gas are found in discrete pockets that are not
obviously connected to one another. Where there are numerous bed dips or altitudes, this may happen.
Deposits are frequently found beneath salt domes or fault planes, where the driller is subject to greater
technical risk. Salt domes can be avoided, and equipment pressure along fault lines can be reduced, by
drilling horizontally.
The reservoir extends down diagonally, making it difficult to drill or locate the "deep end" vertically and
potentially yielding nothing at the "shallow end."
Although the reservoir is connected, the connection is quite asymmetrical, with deep dips and a series of
bars.
Making a land rig, then drilling out into the sea or beneath a lake, would be viable. This would be safer
and less expensive.
These "irregular" reservoirs are actually quite common. As technology advances and there are
comparatively fewer discoveries of elephant reserves, directional drilling is becoming more and more
important.
In the case of an uncontrolled, or "wild well," directional drilling has another function. How can you cap
a well if you imagine one that has ruptured the blowout preventer and is gushing?
The level of subsurface pressure affects this. In some cases, a second control well is drilled to intersect
the same region of the reservoir that the first wellbore did. The new directional well can be filled with
kill fluid once it has been finished.
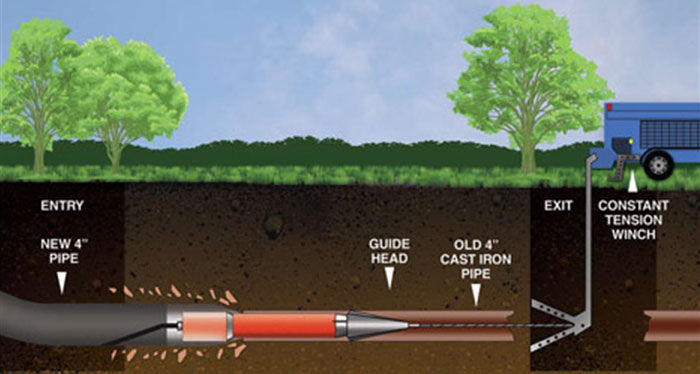
A relief well can help to discharge gas so that the original gusher's strength decreases and can be
controlled if the well pressure isn't too high. To manage and restore appropriate functioning to the
initial well, mud and water are pushed in from a different angle.
Conclusion
The HDB process begins with the surveyor determining the exact location of the underground
infrastructure. The surveyor will then mark the beginning and end points of the project. The drillers will
then use a rotary drill to bore a pilot hole between the two points. A reamer is then used to enlarge the
hole, allowing it to be pulled back to the desired location.
The advantages of HDB include minimal disruption to the environment, cost savings, and a faster
installation time. Horizontal directional boring is also ideal for installing long-distance infrastructure, such as pipelines or power
cables.
HDB is an increasingly popular trenchless construction method and is used for a variety of applications,
from water and sewer lines to telecommunications and electrical cables. It is becoming increasingly
popular for commercial and residential projects due to its cost-effectiveness, minimal disruption, and
speed of installation.
Comments